Sampling tools Comparison
Using accurate Tools drives Massive Efficency Gains for Farmers
Hydraulic Probe
Problem 1: Bucket Looses Soil
Not all of the core makes it into the bucket – you can see it flying out in this slow motion clip.
Problem 2: Frame Rises Inconsistently
The probe moves down a fixed distance from the frame, and this distance can be calibrated for a specific amount of rising.
However, the amount the machine rises changes from core to core depending on the soil hardness and moisture content, so it can capture a different depth of soil every time, no matter how it’s calibrated.
Problem 3: Probe Design Restricts Soil Flow
Large sections of the core are missing. The probe has no way to pierce crop residue, so leaves and husks on the surface gunk up the entrance and restrict soil flow.
The probe also doesn’t have much interior relief (space for the soil to expand), which means that when soil encounters the probe, it’s more likely to be pushed off to the side than to rise up in the core.
Auger
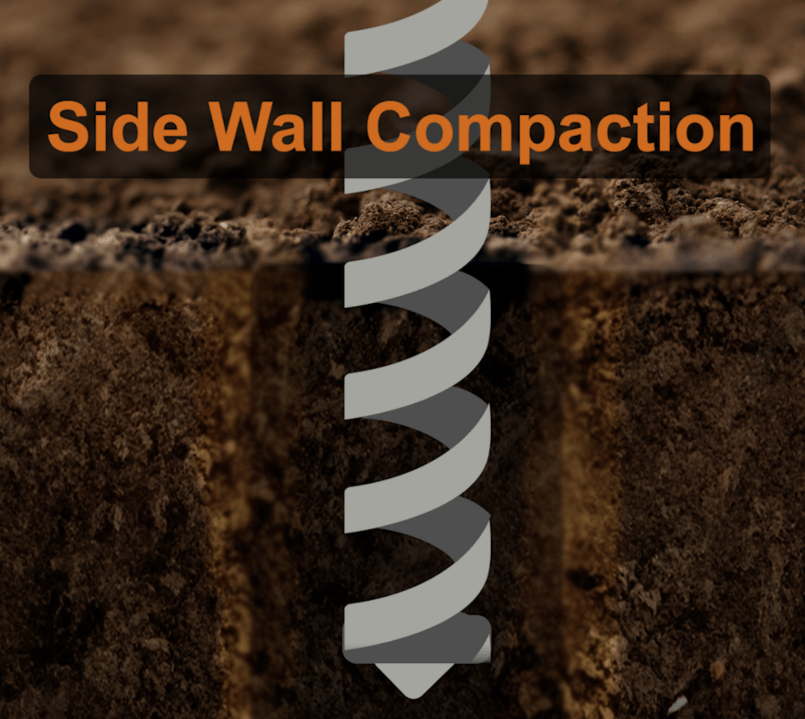
The deeper an auger gets, the more the friction exists inside it, which increases the soil pressure. The side walls are like a sponge (especially in wet soils), so when pressure rises it’s often easier for soil particles to be sucked into the side walls than to push the soil on top of them up and out of the auger.
Some augers, especially if their flights are thinner, wear out to quickly (we’ve seen augers 1″ wide at the surface but 0.5-0.6″ wide at the tip). Others rotate too quickly, which reduces compaction, but causes more soil to fly off the auger’s sides and tip.
This means not all the soil is captured, and the sample doesn’t accurately reflect the soil.
Hand Probes
Mechanical Problems with Hand Sampling
- Core Depth
- Partial Plugs
- Location Error (iPad GPS)
- Location Error (Human)
- No Accountability
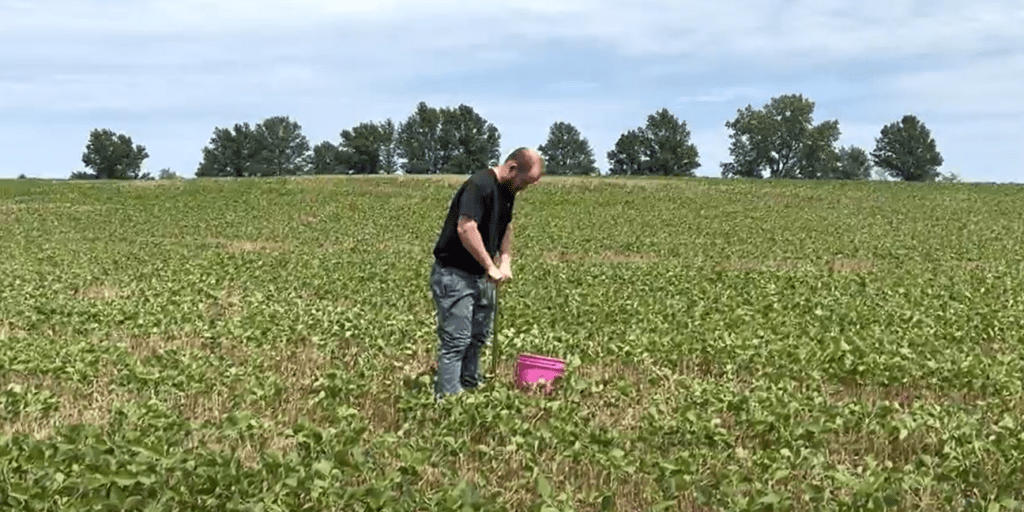
ROGO
ROGO Mechanical Analysis
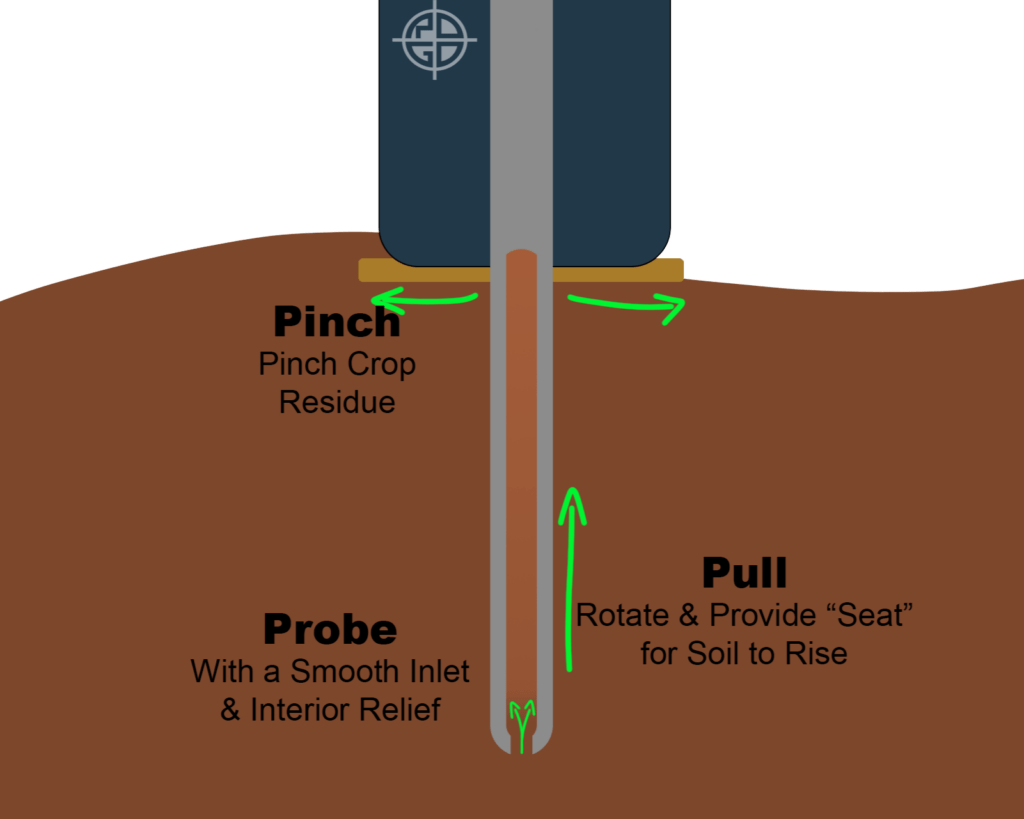
- Ground-referenced depth control
- Uses special techniques to pinch, probe and pull
- RTK-level GPS
- Digital data trail of all field activity
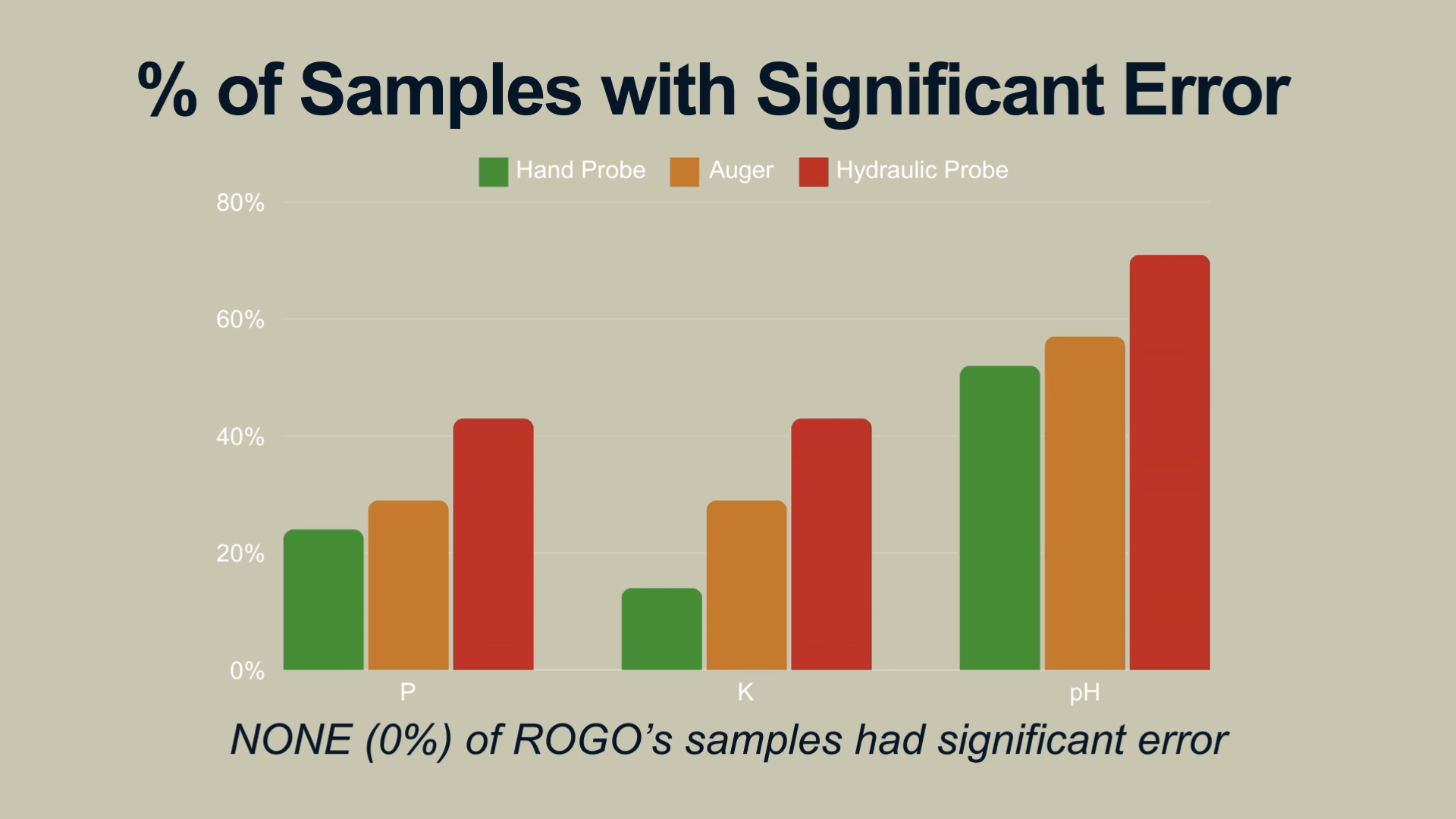
Request the Raw Data
Ready To Get Robotic Sampling On Your Acres?
Give us a call to have your acres sampled robotically this season and get more accurate results
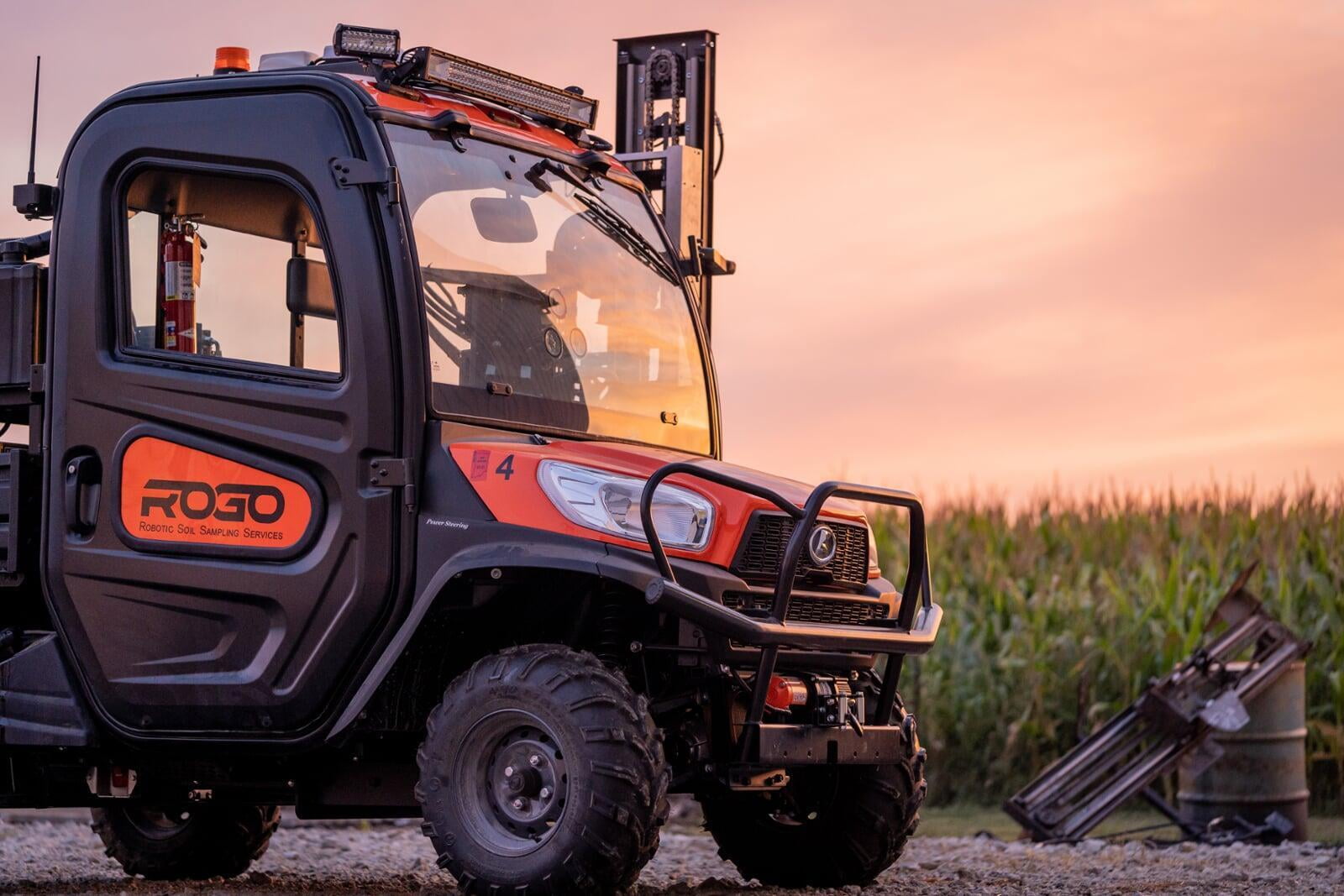